Architects: ChenChow Little
Balmain House is a wonderful example of engineering excellence in residential design and construction. The project involved excavation depths of 10m; design of sandstone sea-walls fronting Sydney Harbour; remediation of an 1880’s sandstone heritage-listed cottage; expressed timber framing; a steel-framed tension-tie roof and a steel helical stair; off-form cast-insitu concrete; heated polished concrete floor toppings; bespoke structural furniture; steelwork; and to top it all off, a 5m cantilever floor plate, hung from curving off-form concrete walls.
Engineering design and documentation for the project commenced in May, 2015. Construction on site commenced in July 2016 and the project was completed in May, 2019. Partridge were appointed as the structural, civil and hydraulic engineers to deliver the analysis, design, documentation and site supervision to support the architect’s design and provide a landmark dwelling.
Creativity & Innovation
This project required creativity and innovation from its very conception. The architectural design called for a maximum floor thickness zone of 450mm (including finishes) to achieve a 5m cantilever that supported slender, two-storey high curving walls! However, not only were the walls to be curved laterally but the green roof slab they supported was also to be curved longitudinally in a ramped fashion, imitating the profile of a ski-jump. The northern wall geometry resembled an ‘S’ shape and required substantial engineering judgement and justification to prove the structural adequacy and robustness of the proposal.
The key innovation from an engineering perspective was achieving the 5m cantilever while supporting a concrete floor, walls, and a concrete green roof with minimal deflection. The floor zone available for this was only 450mm – less, in fact, once allowing for finishes top and bottom. To achieve this, Partridge undertook analysis and calculations to determine if the perimeter walls of the dwelling could act as deep beams. This was anything but straightforward, as both walls were curved and the north wall, in particular, had a significant double curvature in the backspan, as well as some significant voids. (See diagram on Page 3). The north wall was also offset 1m to the north off its supporting column and the concrete floor slab needed to have a flat off-form concrete soffit! Partridge used strut-and-tie analyses and design principles to resolve the forces and load path to satisfy ourselves of the structural adequacy of the structure, which meant we needed to rectify the out-of-plane forces in the roof and floor slabs. Partridge opted to utilise the roof slab geometry, which was also curved, to provide additional stiffness and assist in rectifying the out-of-plane forces.
Sustainability
Partridge specified the use of Boral “Envisia” concrete as it reduced Portland cement by more than 50%. This lowered the carbon in the concrete and meant it required less water. The basement and lift shaft walls were constructed using the Dincel system which allow for a lower carbon cost and less steel reinforcement as opposed to reinforced concrete blocks. Timber framing was used wherever the design allowed. The basement levels were ventilated using the stack effect through the drainage areas and wall cavities, and the roof of the new structure was designed and constructed as a green roof. The design also kept as much of the existing structure that we could to re-use and adapt the existing structure rather than demolition and re-construction.
Creativity & Innovation
Creativity and innovation were required in most aspects of this project. The concrete’s capacity was pushed to the envelope in many places (both figuratively and literally, noting the stresses and high stiffnesses required), and few, if any of Partridge solutions came “out of the box” or relied on standardised details. Bespoke steel columns were conceived and fabricated for the glazing columns; concrete had to be detailed and reinforced to accommodate deep recesses and rebates in areas of high stress and the slabs and beams were analysed, shaped, and reinforced in ways not seen or encountered previously.
Built Environment, Heritage & Value
The site is prominently located on the peninsula of Balmain East with north-easterly views directly of the Sydney Harbour Bridge. The original 1880’s heritage sandstone cottage was remediated and restored to reinstate its original balcony features and façade details.
The new dwelling adjacent was designed as a modern, off-form concrete structure to clearly delineate the construction eras and technologies. The finished dwelling honours the heritage of the original structure whilst providing a modern family home fit for a prominent site on Sydney Harbour’s foreshore. The structure now has the ability to last for another 100 years or more!
Elegance & Detailing
Significant detailing challenges arose from the extensive use of cast-insitu, off-form concrete. Careful consideration had to be given to controlling shrinkage and cracking, as well as needing to carefully consider pour sequencing and construction joint locations – yet concealing the unsightly joints where intersecting elements from different pours interfaced. There were two external downpipes which we utilised to hide the contraction joints. However, all other locations – including the tops of the walls – were visible elements, thus the pour joints and contraction joints had to be carefully co-ordinated into the design in close collaboration with the architect. Partridge identified and specified a concrete mix design that was not just more sustainable, but provided reduced shrinkage properties, thus allowing us to push the limits in terms of jointing to meet the structural beam requirements. The reduction of joints (whilst still eliminating shrinkage cracks) eventuated in an outstanding visual result not typically encountered with off-form concrete structures of this size.
Ease of Constructability
A major challenge involved site access constraints, which the builder was initially at a loss to overcome, save for troublesome barge access from Sydney Harbour. Partridge suggested and went onto design and specify temporary foundations that would facilitate the use of mobile cranes for bulk site deliveries, and to establish a tower crane. This allowed for several key items to be pre-fabricated off-site (such as the helical steel stairs) and then delivered and installed in rapid fashion onsite.
Street frontage and parking was non-existent so Partridge designed and detailed a temporary works platform at street level for site deliveries. This was adjacent a 10m excavation for the site, and thus we designed a vehicular crash barrier for safety.
Architects: ChenChow Little
Builder: Beebo Construction
Photography: Dark Fox Photography and Peter Bennet Photography
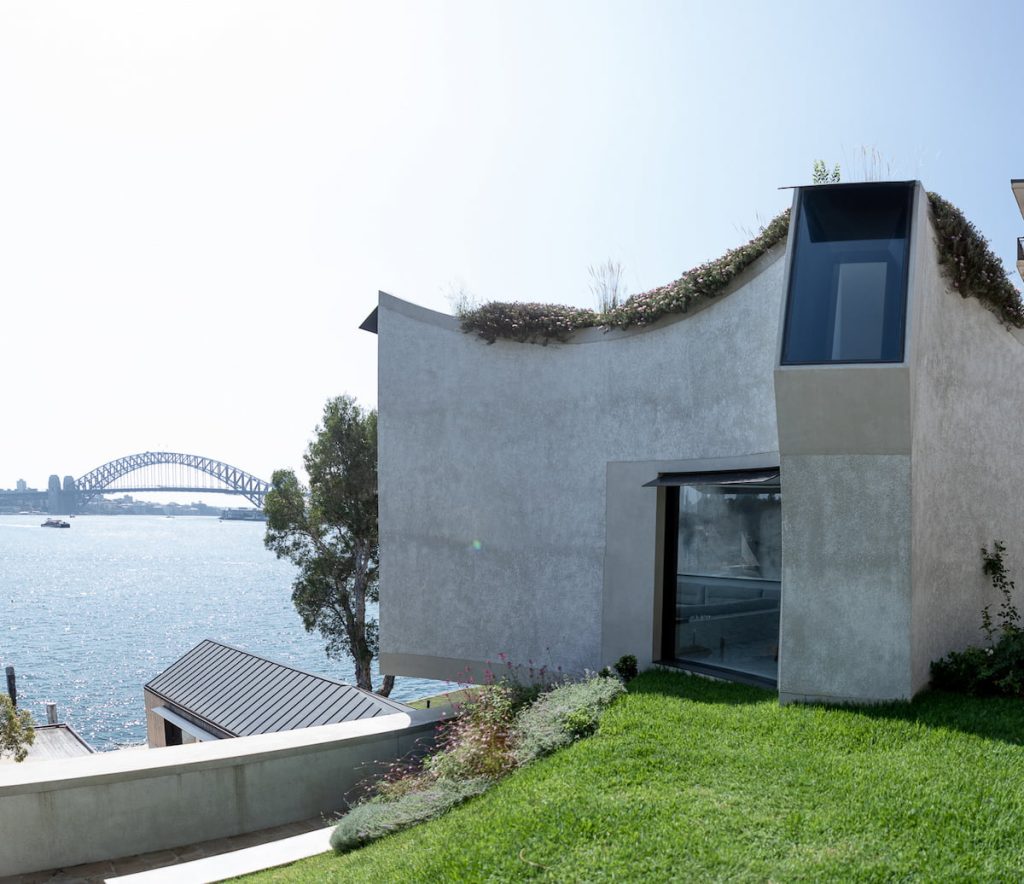
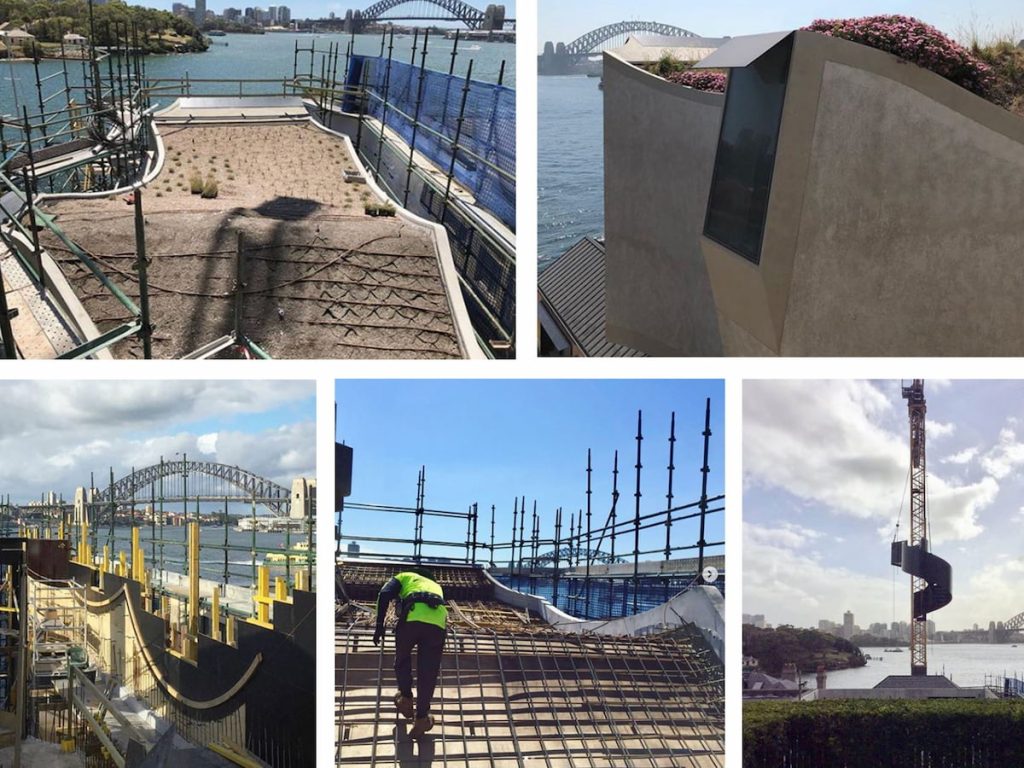