Halo is a major public artwork installed at Central Park, Sydney and winner of the ACSE Structural Engineering awards 2013 and Engineers Australia Engineering Excellence President’s Award 2012. Its 12m diameter ring is eccentrically supported by an inclined post, 15m in height. The impressive 12m diameter ring powered by the wind, rotates consistently, while yawling somewhat languidly. The project required innovative techniques in management, design and fabrication. A highly specialised team of engineers, fabricators and specialists came together to produce this artwork envisioned by the artist.
Central Park is the visionary redevelopment of the old Carlton & United Brewery site, bordered by Broadway and Abercrombie Streets in Chippendale and occupies nearly six hectares of the southern Sydney CBD, defining Sydney’s ‘downtown’. The modified concept master plan for this rare site was approved by the NSW Minister for Planning in February 2009, and includes the protection of heritage buildings, new parklands and community facilities and substantial upgrades to urban infrastructure. The expansive site allows for the development of approximately 235,000 sqm of residential, commercial and retail space. Around 1900 residential apartments may be built on the site, delivered over 3 – 10 years. The major new residential tower of this development has been designed by Frenchman, Jean Novell, one of the world’s leading architects. This building, of the same height as the main tower of UTS but bulkier, would have overshadowed the large central public park and so a large cantilevered mirror extending some 35m out from the top of the tower and heliostat will capture sunlight and reflects it down onto the landscaped terraces, and park below. It was recognised by the City of Sydney Council and the developer Fraser Property Australia that this adjacent public park needed a major art piece as a central focal point.
Frasers commissioned Jenny Turpin and Michaelie Crawford of Turpin Crawford Studio, pre-eminent Australian artists specialising in kinetic works activated solely by the forces of nature. They wish, by the movement in their art works, to allow those natural forces to be clearly demonstrated and felt within the viewer. Their work in this way parallels the focus of structural engineering goals. Whilst they perceive these forces of nature emotionally and seek to bring them to life visually for the public, engineers formulate these same loads and mathematically calculate the precise members and materials needed to withstand those force in order to allow a built environment which houses and protects the same public. Interestingly the old brewery pictured was the original inspiration for the artists.
Turpin and Crawford wished for an engineer who would be able to work with them in this way and approached Partridge to be responsible for the full Project Management, Structural and Mechanical Design, the Artists’ design process, the fabrication, testing, installation and commissioning of this unique piece of art.
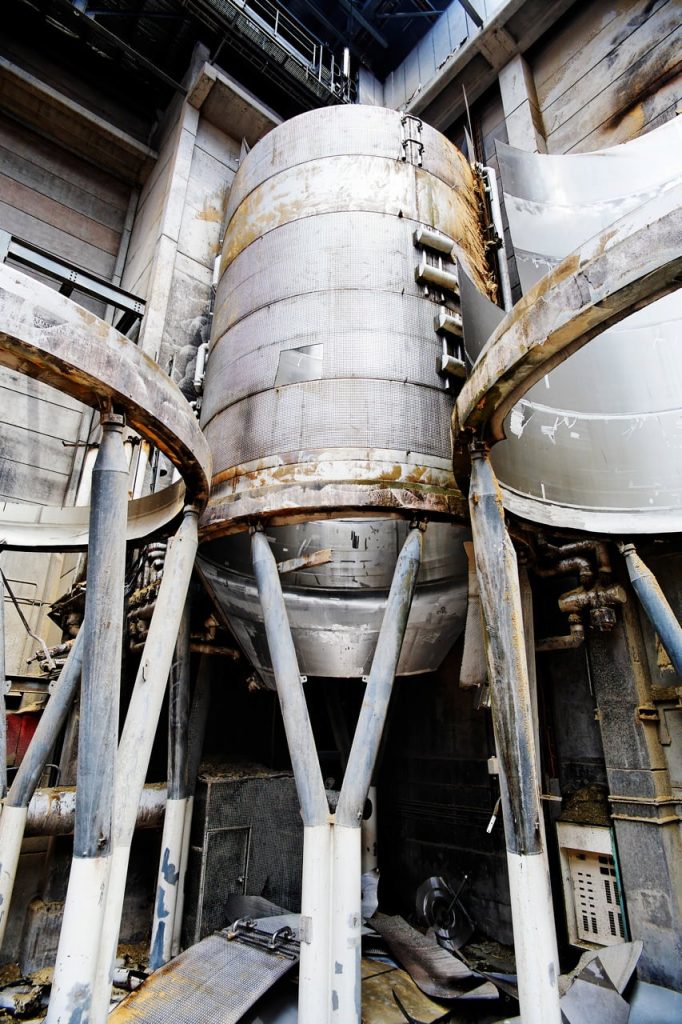
Halo was conceived by the artists as a large (12m diameter) ring eccentrically supported by a single, inclined ‘spoke’ to a slightly tilting and tapered post, 15m high. They required that the ring would not only rotate in the gentle breezes but would also pitch and yawl and, of course, be stable under maximum wind gusts. The movement was to be ‘languid’, and as the central object in the common area to give the viewer, who may be resting or playing in the public park, or looking down on Halo from the many apartment windows, the opportunity to connect with this slow and gentle movement and so, perhaps, to enable an escape for a time from the usual rush of city living.
Partridge immediately recognised the complexity of the project and the need for rigorous planning. Since very few similar projects like this had been attempted previously in Sydney, and no public art work of this scale and complexity, there was no clear precedent for Partridge to follow.
A schedule was created that reflected the need for a significant research and development period, prototype testing, full-scale testing and fabrication. The schedule reflected the tasks required by the project management, artist, engineers, fabricators, and installers. Partridge, after discussion with all others who would be part of the design, test, fabricate and build process estimated 6 months for completion of the project. This involved approximately 4 months of research and development, overlapping with a month of testing and finally 2 months of fabrication and installation.
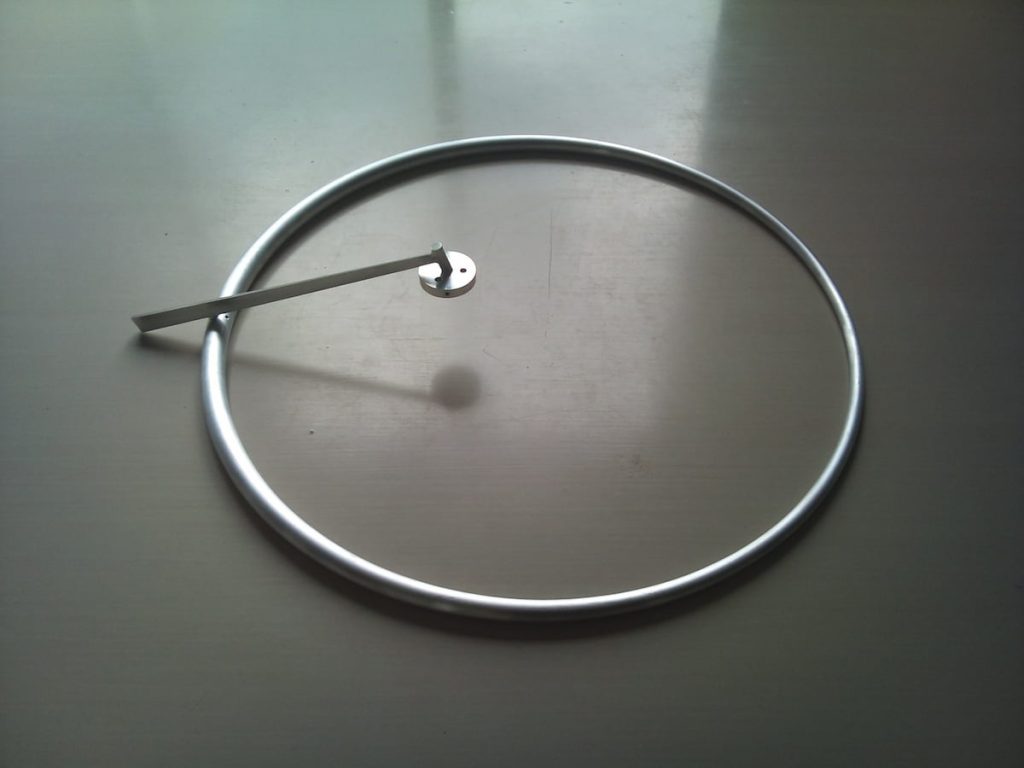
Partridge adopted fully collaborative based, hands-on approach to ensure a complete “immersive” management of the project. This involved being closely involved with all aspects of the project and having all teams closely involved which each other’s work. The aim was to have all parties to have some level of control and some ‘ownership’ over the final product. Essentially every member of the team was promoted to become an artist in his or her own right.
“l found the creation of a friendly environment within the team was quite innovative. It helped sharing thought knowing and respecting each other role in the project. It was particularly important to ensure that the vision of the Artists could become reality with no compromises. ” —Valerio Corniani, Composite material engineer.
Inherent to a 15 m high kinetic artwork were several challenges that Partridge identified in the early stages of the project. Partridge overcame these by engaging professionals to find innovative solutions for the design of the project and to collaborate to find the most effective solution. Engineers in wind, mechanical, composite material design were independently engaged in the design of Halo. Partridge established a co-operative and inclusive working environment with this divergent group of professionals which encouraged and prompted everyone involved to not only design their particular aspects of Halo but to also provide additional input and ideas into the final product – often across their usual discipline boundaries.
The turning, tipping and yawl movements of the Halo are dependent on the site wind speeds. Predominately light wind speeds were found for the whole site by CPP wind engineers. In order for the ring to be excited by these typically lower wind speeds, it was realised that the moving ring and arm had to be very, very light in order to create the maximum effect in these conditions. Initial designs in steel indicated that the inertia would be too great for movement to occur in any except the stronger winds. This then suggested a carbon fibre design would be explored. Partridge engaged Gurit, an international consultant and manufacturer of exotic materials with extensive experience in yacht and wind turbine design. Gurit became part of the team and worked in an iterative design loop with the other members to reach the final solution of a 500mm thick, 12m diameter ring with a carbon weight of less than 500kg – an extremely light result for the size of the work.
It was not only essential to the artist that Halo was a moving work of art but also the manner in which it moved. The artist had envisioned that Halo, in its turning motion would have only one-way rotation, that is, no ‘weather vaning’ could be allowed. This was very difficult to achieve as almost inevitably, when subjected to a wind flow, objects will find a neutral position and either point into the wind or away from it. Partridge engaged Graeme Wood of CCP Wind and together tried numerous working models within their wind tunnel. These consisted of all manner of variations of small scoops, eccentricity of fulcrum and differently-shaped and differently-angled arms. This involved the building of several dozen 1:10 models in wood and/or aluminium, and over a hundred hours of testing in the wind tunnel. Throughout this whole lengthy process, a working group of the artists, Partridge and CPP Wind engineers engaged in a collaborative approach so that all parties would be satisfied of the result within their own particular area of competence. Finally, the team achieved a result that all were striving for – a 12m ring of a diameter tapering from 550mm to 300mm and with a scooped, eccentric arm projecting past the ring. This model did not vane, it rotated consistently, and it yawled somewhat languidly. Actual wind forces at all wind angles were obtained from these tests, which when combined with the general wind behaviour which had also been modelled for the overall site, allowed a precise engineering design.
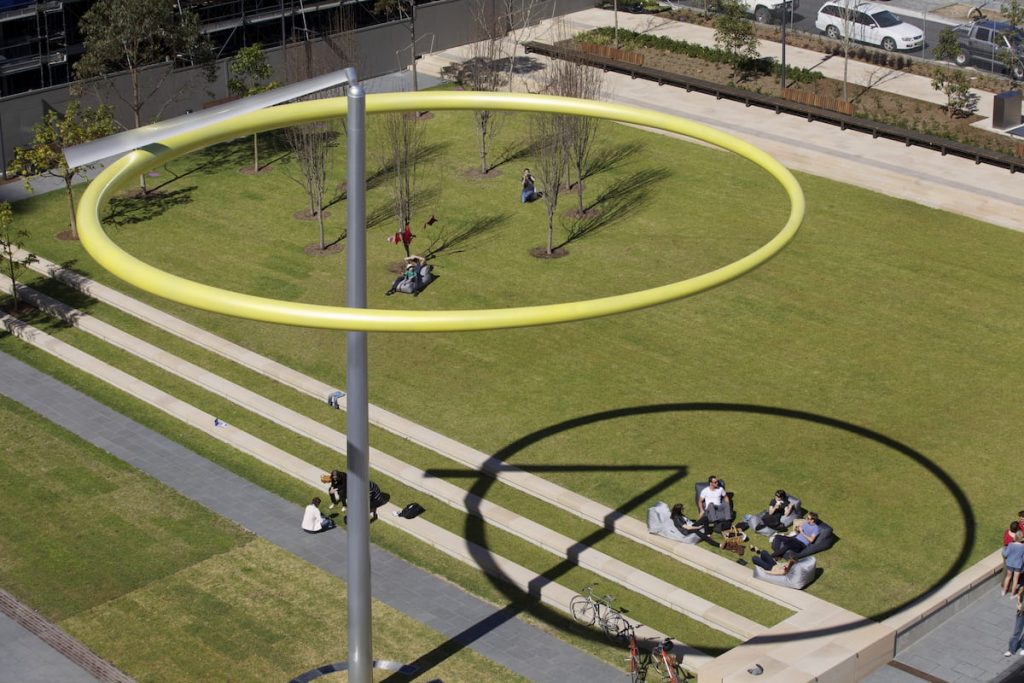
Halo demonstrates how professionals from very disparate disciplines and backgrounds can form a cohesive and collegiate team to enthusiastically push each other to achieve remarkable results. Not least of these was the determination that the clients and artists’ wishes and hopes were to be given paramount importance. Partridge recognised from the outset that no amount of clever or innovative engineering would be of any value if the artists were not content with the final outcome.